Sealants are an essential tool in the construction industry. A sealant is a substance used to block the passage of fluids through the surface or joints of materials. They also prevent the passage of air, dust, noise, or contaminants into or out of a structure. Not to be confused with sealers which form a thin surface layer and may penetrate to provide surface protection when sealants are primarily used for filling voids, gaps, cracks, and joints. There are a variety of sealants each with different purposes and properties. We’ll discuss many of the most popular sealants.
Caulking
Caulking is used primarily in construction and home improvement projects. It is typically a flexible material that is applied to seal gaps or joints between building materials such as wood, metal, glass, or masonry. Caulking helps to prevent air, water, dust, insects, and noise from entering or escaping through these gaps. Caulking sealants are made from various materials, including silicone, latex, acrylic, polyurethane, and butyl rubber, among others. Each type of caulking has unique properties and is chosen based on factors such as flexibility, durability, adhesion, and resistance to weather and chemicals. Some of the most common ways that caulking is used are:
- Sealing gaps around windows and doors to improve energy efficiency and weatherproofing
- Filling cracks and joints in walls, ceilings, and floors to prevent water intrusion and air leakage
- Sealing joints in plumbing fixtures, such as sinks and bathtubs, to prevent water leaks
- Caulking around trim and molding to provide a finished look and seal gaps

Joint Fillers
Joint fillers are used to fill joints and gaps between building materials or structural elements. These fillers can provide structural integrity, preventing moisture or air infiltration, and/or enhance the aesthetic appearance of surfaces. Building concrete pads requires the inclusion of control and/or expansion joints in which joint fillers are often used. These joints are necessary to prevent cracking of the concrete pad and a variety of joint fillers are available to fill these voids. Each joint filler option has certain properties so it’s important to consider the nature of the application when choosing which product to use. There are 3 types of joint fillers, those types being epoxy, polyurea, or polyurethane.
Epoxy joint fillers are formulated from epoxy resins and a hardening agent (often a polyamine or polyamide), which undergo a chemical reaction to cure and form a durable, strong bond. Freezing temperatures will prevent epoxies from completely curing. Only use epoxies when the installation temperature is above 32 degrees F (0 degrees C). However, on a positive note, if a joint filler is improperly installed (i.e., filled less than full depth, has concave profile) or if it must be removed for other reasons, epoxies are removed very easily. One application for epoxy joint fillers would be filling joints in a newly placed concrete floor or for repairing deteriorated joints in an existing floor. Form & Build has plenty of epoxy joint fillers to ensure we can help any job. One of them would be the W.R. Meadows Reziweld which you can see online by clicking here, plus many others.
Polyurea joint fillers are a type of elastomer that forms when an isocyanate reacts with a resin blend component through a process called step-growth polymerization. They are known for their fast cure times, flexibility and durability, and resistance to chemicals and abrasion. Due to their durable nature and resistance to environmental factors, polyurea joint fillers typically require less frequent maintenance and replacement compared to other fillers. They provide long-lasting protection and performance in challenging environments (such as below 0 degrees C). An application for polyurea joint fillers would be anything that is a fast track construction project such as most things that involve exposed concrete to adverse weather conditions, as their quick cure times can allow access to other building trades in one hour or less from the time of placement. Form & Build often recommends the Formex CanSeal Joint Filler (JF) as a go to polyurea joint filler. You can check it out online by clicking here and can see more polyurea joint fillers on our site too.
Polyurethane joint fillers are formulated from polyurethane resins, which undergo a chemical reaction to cure and form a durable, flexible seal. They are known for their adhesion, versatility, and paintability as many polyurethane joint fillers are paintable once cured, allowing for seamless integration with the surrounding surfaces and enhancing the aesthetic appearance of the joint or crack. Applications for polyurethane joint fillers would be bridge building, automotive coach building, and many other professional industries, as its hard wearing approach and exceptional adhesive properties means it works well for professional applications where strength and speed are crucial. Form & Build carries many different polyurethane joint fillers. We are proud carriers of the always popular Masterseal NP1 Polyurethane joint filler, and you can check it out online by clicking here and also seeing our polyurethane joint fillers.
Self-Leveling
Self-leveling sealants are a type of sealant that is formulated to flow and settle into horizontal joints or gaps without needing tooling or smoothing by hand. This allows them to create a smooth, level surface without the need for additional tooling or manipulation. Self-leveling sealants are commonly used in construction and renovation projects where flat; level joints need to be sealed, some examples being:
- Filling control joints in concrete floors or slabs
- Sealing expansion joints in driveways, sidewalks, and parking structures
- Repairing cracks in concrete floors or walls
- Sealing gaps around plumbing fixtures, windows, and doors in horizontal surfaces
Self-leveling sealants have many applications. They are engineered for use on control joints, expansion joints, asphalt to concrete joints and crack filling including exterior balconies, concrete floor slabs, concrete and asphalt driveways, roadways, walkways and pavement, garages, roofing, patios, pools, fountains plus even other applications. Form & Build of course, is the place to go for all sealant needs. We recommend the Formex CanSeal Self-Leveling (SL) Sealant as our self-leveling sealant of choice. You can see for yourself online by clicking here plus many other similar sealants. The CanSeal SL and NS are often confused with being polyurethane, however, they are different. CanSeal is a:
- Softer, hybrid blend that gives it unique properties
- Such as can be used in cooler temps, no primer needed in damp applications and has a superior bond
- Fast curing, paint compatible, and non-silicone, solvent free
- Comes in grey and black
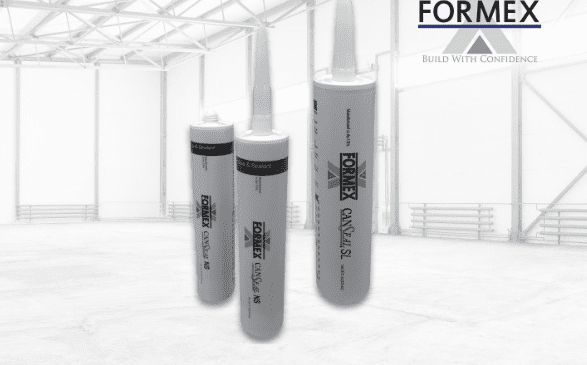
Sealants are a staple of the construction industry and so long as there are joints, there will be sealants. As you can see, there is a variety of sealants for a variety of uses. Lucky for you, Form & Build is the one stop shop for all your sealant needs. You can browse our complete list of sealants online by clicking here and get a quote online today. You can also call one of our 6 branches to speak with a representative that is happy to help today!